Why Are Ded Processes Particularly Suitable For Repair?
What is Directed Energy Deposition?
Directed Energy Deposition (DED) is one of the vii categories of Additive Manufacturing processes. DED forms 3D objects by melting cloth as it is existence deposited using focused thermal energy such every bit laser, electron axle or plasma arc. Both the energy source and the material feed nozzle are manipulated using a gantry system or robotic arm. DED is increasingly used in hybrid manufacturing where even the substrate bed is moved to create complex shapes.
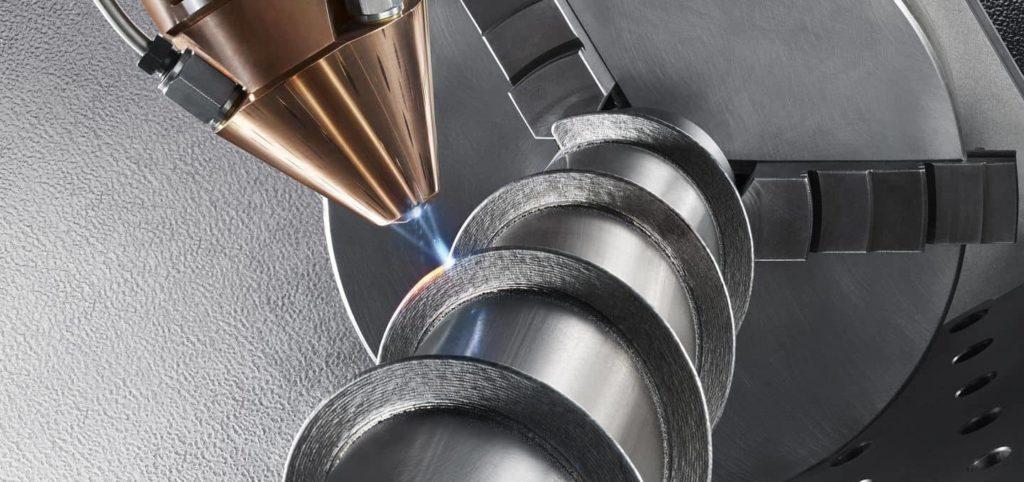
Although it's possible to create parts from scratch, due to the nature of how the DED engineering science works, currently its predominately used for repairing by calculation material to an existing part such as turbine blade repair.
Directed energy deposition was developed by Sandia National Laboratories in 1995 under the name of LENS (Laser Applied science Net Shape) and then was commercialized by Optomec Blueprint Visitor.
Due to the variations in the energy source and final use, DED is sometimes referred to as laser metallic deposition (LMD), 3D light amplification by stimulated emission of radiation cladding or direct light fabrication.
Directed energy deposition types
Although DED technology can be used to make metal, ceramic and polymer parts, it is predominately used to make metal parts. DED can be classified into the following groups by the energy source information technology uses to melt cloth.
- Laser-based DED systems such as Optomec'south Laser Engineering Internet Shape (LENS) DED system uses a light amplification by stimulated emission of radiation as the master free energy source
- Electron beam-based DED systems such every bit Sciaky's Electron Beam Additive Manufacturing (EBAM) use an electron beam to cook the powdered material feedstock
- Plasma or Electric arc-based DED systems such every bit Wire arc additive manufacturing (WAAM) DED process uses an electric arc to melt the wire
Directed energy deposition engineering can likewise be subdivided further into the post-obit types based on the types of material feedstock used to create the parts.
- Powder-based DED systems such as Light amplification by stimulated emission of radiation Engineered Net shaping (LENS) or Laser metal Degradation (LMD) feed powder through the nozzle and melted by a laser beam or electron beam
- Wire based DED systems feed wires through a nozzle and use laser, plasma arc or electron beam to create the molten puddle
How does Directed energy deposition piece of work?
Different types of DED systems discussed in the previous section work marginally different from each other. Still, the core principle can be explained using the in a higher place powder-based laser DED system.
Since the process creates a molten metallic pool, the DED process typically occurs in a hermetically sealed sleeping room either, filled with inert gas for light amplification by stimulated emission of radiation and arc energy source or vacuum for electron axle systems to finish metal oxidization, especially for reactive materials like Titanium.
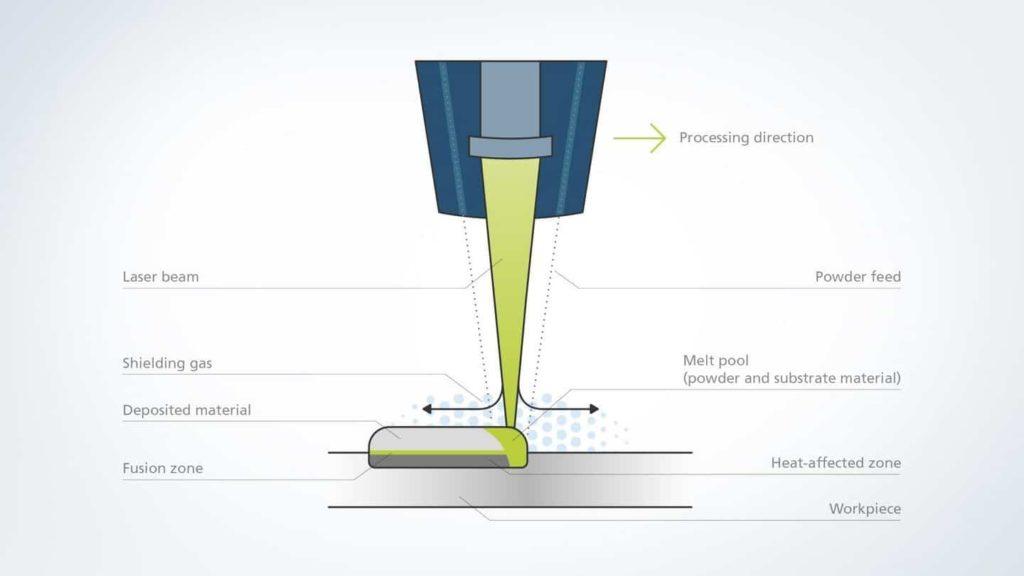
The centre of a typical DED system is the nozzle head (figure ii) which consists of the energy source and the pulverization delivery nozzles which converges at the point of eolith where the laser axle is focused. Nozzle head is mounted on either a multi-axis CNC (Computer Numerical Control) head or an articulated arm. Typically, the build platform is part of the multi-centrality CNC arrangement which includes the nozzle head.
- Using the geometric CAD information, both the nozzle head and the build platform is moved to generate the 3D geometrical features
- The laser beam melts the surface and creates a small-scale molten pool of the material on the substrate at the start point forth the build path
- The feeders feed the powder through the nozzle into this molten pool
- Using the CAD geometric information, CNC controlled caput or the bed or both are moved along the build path to creating the metal part characteristic
credit:BeAM
Material suitability
Predominantly, DED uses metal in the form of either wire or powder. Nevertheless, DED technology is also capable of using polymers and ceramics. For example, Arevo makes composite frames using polymer and filament of carbon fibre.
DED supports a wide range of metals as whatsoever metal that can be welded tin can exist used to create parts through this technology. Commonly used materials by various manufacturers are equally follows;
Titanium and Titanium alloys | Niobium |
Inconel 718, 625 | Stainless Steels (300 serial) |
Hastelloy | Aluminium alloy 2319, 4043 |
Tantalum | Zinc alloy |
Tungsten | Copper-Nickel alloys |
Typical directed energy deposition applications
DED is already utilised in central industries similar aerospace, defence, oil & gas, as well every bit the marine industry, for example, shipping frames and structures, refractory metal components, ballistic material tooling repair and reconditioning and marine propulsion, etc.
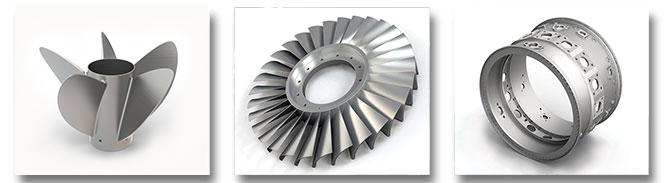
Like any other subtractive manufacturing process, parts made using DED can be heat-treated, hot-isostatic-pressed, machined, or finished in whatever customary manner, which opens various new applications. Almost of the hybrid manufacturing systems utilise DED and accept increased in popularity.
Advantages and disadvantages of directed energy deposition
DED technologies are used exclusively in metallic additive manufacturing due to the nature of the procedure and are ideally suited for repairing or calculation material to existing components.
Advantages of DED
- High build rates – DED's higher deposition rates at relatively low resolution means faster build rate compared to some other metal additive manufacturing process
- Dense and strong parts – DED creates higher density parts hence their mechanical properties are as good every bit cast or wrought material
- Near net shape – Parts can be near internet shapes requiring a minimal amount of post-processing
- Can exist used for repairing – Ideally suited for application requiring metal improver to existing parts hence lends itself for repairing applications
- Multi-cloth range – Latest DED machines have the capability to accept several different powders or wire containers which enables to build parts with custom alloy
- Larger parts – Comparably larger parts can exist built using DED. For case, Sciaky's EBAM printers take the capability to print parts a few meters high
- Easy textile change – Since the material is fed during the process on demand from split up powder containers, it's piece of cake to refill or alter the material
- Reduced material waste product – DED but deposits the material it needs during the process pregnant, less wastage compared to processes like powder bed fusion (SLS and DMLS) where the total build platform has to be filled with metallic powder
Disadvantages of DED
- High capital cost – Direct energy deposition systems are comparably very expensive to the other types of metal additive manufacturing systems
- Low build resolution – Parts produced using DED technology are lower in resolution with a poor surface finish. It will wait like sand or investment castings and would require secondary processing such as machining or aqua blasting, hence adding more fourth dimension and cost
- No back up structures – Due to the nature of how the DED technology builds parts, back up structures cannot be used during the build process, hence features like overhangs will non be possible
Source: https://engineeringproductdesign.com/knowledge-base/direct-energy-deposition/
Posted by: longtraccivo.blogspot.com
0 Response to "Why Are Ded Processes Particularly Suitable For Repair?"
Post a Comment